从汽车诞生之日起,超级跑车就代表着一种梦想,希望和热忱,同时为汽车的升级进化不断提供技术资源。2000年,曾参与开发性能车Celica的工程师棚桥晴彦和首席试车手成濑弘,在雷克萨斯内部召集了一群顶尖的工程团队,秘密展开了“究极国产超跑”研发计划,从一开始就将目标定为创造前所未有的感官体验。历经十年磨剑,LFA量产版于2010年正式上市,其以超强的性能、超越传统的创新制造工艺以及致力以声浪感动世界的特质,成为当代独一无二的超级跑车,并成为雷克萨斯F高性能家族的精神图腾。LFA以限量500辆的方式,于2012年12月14日圆满地为自己画上了句号。虽然只有小部分幸运者才能享受LFA的梦幻表现,但就像棚桥晴彦所坚信的-“LFA的精神将成为每个雷克萨斯爱好者的骄傲所在”。
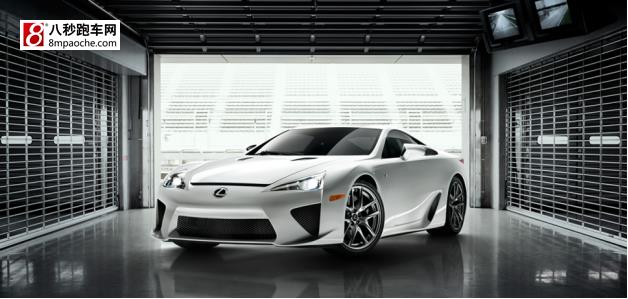
LFA是LEXUS雷克萨斯自品牌成立后所研发生产的首款超级跑车。获益于丰田在F1赛事中所积累的丰富经验,总部设在科隆的TMG(Toyota Motorsports Group GmbH)为这款超级跑车的动力单元提供了基础设计,并在其后负责气缸盖的铸造。这台最终由雷克萨斯与雅马哈合作完成的4.8升V10自然吸气发动机传承了F1赛车引擎的极致性能,能够在8700转/分时,输出 560马力的最大功率,并在6800转/分时提供480牛•米的峰值扭矩。从怠速状态到转速升至9000转/分,仅需要0.6秒,不仅仅是性能出众,雅马哈还为之创造出了激动人心的特殊音色-天使的咆哮。搭配6速ASG变速箱,采用前中置发动机后轮驱动的LFA,从静止到100公里/小时的加速时间仅需3.7秒,极速状态可达325公里/小时。为了实现最佳的轻量化效果,LFA的底盘使用65%的碳纤维增强复合材料和35%的铝合金打造,全车仅重1480公斤。2011年,基于LFA普通版开发的LFA纽博格林版在长达20.6公里的纽博格林北环赛道创造了7分14秒64的圈速。
传奇的名字
实际上,LFA在内部计划时并没有任何带有意义的名字,仅被称为P280项目。由于这款概念车需要在2005年的底特律车展展出,同时概念车应该严格遵循雷克萨斯为概念车所制定的命名原则,必须带有“LF”,即“LEXUS Future”,所以,考虑到这款超级跑车项目的前瞻性,设计团队便为其加上了代表Advance意义的“A”,这便是LF-A名称的由来,即Lexus Future-Advance。
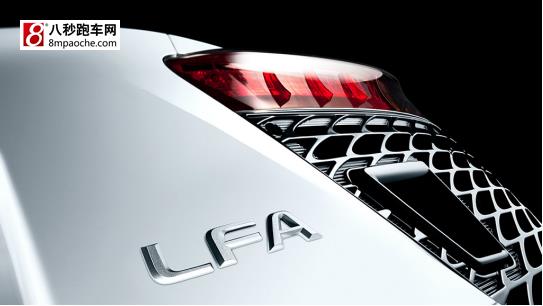
四年后,LFA亮相东京车展,此时概念已经成为现实,因此LF-A中间的横杠被去掉,最终这款旷世超跑被赋予了一个堪称传奇的名字-LFA。
175人的专属工厂
为了满足LFA严苛的生产条件,位于丰田市的元町工厂被改建为LFA的专属工厂。虽然它有机库那么大,但是这里看起来更像一间高级汽车美容店而不是一座工厂。与此同时,在雷克萨斯所有能工巧匠中挑选出的175人,组成了雷克萨斯历史上最强大的精英团队。他们是制造这500台超级跑车的关键,他们的做事方式集中体现了雷克萨斯的品牌宗旨,即:通过将开创性的科技与手工工艺相结合,打造出以驾驶员为中心的豪华汽车。
10000个零件的绝妙组合
每一辆LFA都由10000多个零部件装配而成,包括发动机、传动系统和车架。当然,一切都从最基础的材料-碳纤维开始。
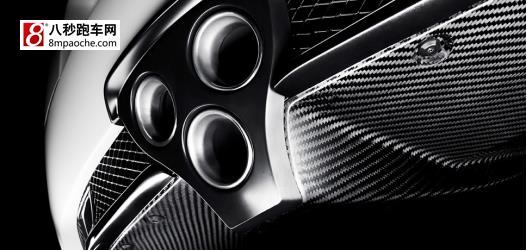
碳纤维的制造由特制的三维碳纤维编织机也就是现在已经非常著名的雷克萨斯“织布机”承担。这种机器能够将碳纤维织成厚度不一的管状。由于碳纤维极为复杂的加工工艺,即便配备了全世界稀有的雷克萨斯“织布机”,也仅能每天生产一台LFA的座舱。部分碳纤维原料更需要经过激光切割,然后进入“铺覆”工序-专业人员需要半年时间才能掌握的一种技术。吸饱了树脂的碳纤维板被铺到模具上,用来制作仪表板和侧梁。每一层碳纤维板(最多有 13 层)都需要用手持式吹风机加热,然后用带着白手套的双手塑造成型。每铺一层都需要进行真空密封,以确保它和上一层紧密贴合,中间没有气泡。
如此繁复的工艺加上整个装配过程,一台LFA从0到完成组装需要7天时间。
不允许1/100毫米的误差
一旦LFA车身壳体送去塑型,就需钻出线束和软管的穿孔。而为了在这种新型材料上实现完美的钻孔,雷克萨斯采用了32种不同的钻头来进行最精细、最干净利落的切削,其中一些钻头带有定制的尖头和金刚石涂层。
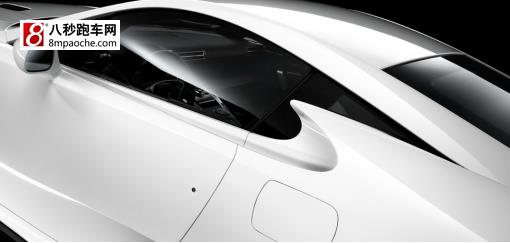
随后,碳纤维车身会被增加额外的负重,以监测强度。并对车身上567个测量点进行针对性测量,以实现高精度的车身制造。而在车身组装完成之后,还需要通过额外的检查:在一个封闭房间内进行,具有专为LFA设计的照明装置。在这里,专家们检查每辆车的外部零部件是否安装牢固、校准完美。如果存在1/100毫米的误差-比如出现在两块车身板件间的缝隙中,也必须经过校准后达到完美状态。
为了保证每一辆LFA都完美无瑕,组装完成超级跑车需要经过5天的测试检验,并且都要交给试车手天野信明-毫无疑问,他的工作是全世界最酷的工作之一-他将在LFA工厂的专属试车道上对每辆车进行性能检验。试车手关注的重点是每辆LFA在时速达到201公里时,整车在七大关键领域的表现,包括:可控性、驾驶感受、声浪、制动性能、功率、噪音与震动,以及零部件功能。如同在道场精修的高手,最终经过重重测试后,LFA们方获准离开这座超级工厂,奔赴500位幸运车主的手中。
碳纤维的胜利
对超级跑车来说,底盘刚性是成功与否的关键。为了与超级跑车的设计保持一致并确保质量达到最优,工程师团队在LFA的关键部位上使用了碳纤维增强复合材料(CFRP)取代常见的铝合金,每一种可用于最大限度提升碳纤维使用效率的方法都经过了仔细的考察和评估。
事实上,LFA除了使用铝合金支架支撑发动机及悬架外,65%的底盘构造均使用碳纤维增强复合材料。在源自F1赛车的碳纤维单体壳座舱里,雷克萨斯使用了三种复杂的碳纤维成型工艺,所有部件均由技艺高超的雷克萨斯技师手工组装。这三道工艺分别是:第一,预浸渍。这是一道手工完成的工序,用热固树脂对碳纤维薄片进行浸泡,经此流程打造出一种非常坚固且稳定的结构。在LFA上,主要用于制造驾驶舱主框架;第二,树脂传递模塑成形工艺(RTM)。RTM工艺使用的是预先成型的碳纤维部件,之后再经过热固性树脂浸处理。它被用在传动轴通道、底板、车顶和发动机盖上;第三,C-SMC(碳纤维片状模塑复合材料)。采用的是借助模具压制成型的短碳纤维,主要用在LFA的后柱和后地板上。严苛的轻量化标准,使雷克萨斯并不放过任何一处可以利用碳纤维部件的细节,包括LFA的发动机舱盖支撑杆在内的许多部件,也全部使用碳纤维制成。
由于LFA的车架由碳纤维座舱及铝合金发动机支架组成,在连接碳纤维与金属部件时不能使用传统的焊接工艺,而需要特别的连接技术。常规连接工艺采用的是包裹在碳纤维增强复合材料内的一个铝制螺纹插件,而LFA则创新性地使用法兰铝环将两种材料连接在一起,因而无需插件或与碳纤维增强复合材料直接接触,降低碳纤维增强复合材料被损坏的可能性。
如此复杂且兼具创新设计的混合车架令LFA受益非凡,LFA的车体仅重1480公斤,比相同时代同样使用V10发动机的保时捷Porsche Carrera GT更轻,为LFA巅峰的加速性能、卓越的操控性能打下了最坚实的基础。为了纪念碳纤维增强复合材料在LFA上的成功应用,LFA的钥匙同样使用碳纤维材料制作,令原本造型普通的钥匙熠熠生辉。
日本汽车史上第一台搭载于乘用车的V10发动机
作为F家族的巅峰之作,超级跑车LFA的动力参照了F1赛车的标准制造。这台发动机由TMG(Toyota Motorsports Group GmbH)提供基础设计和气缸盖的铸造。TMG的前身为Panasonic Toyota Racing,在2001-2009年负责丰田F1赛车的研发和赛事运营。2002年起,丰田首次以厂队身份参与F1赛事,而当时F1赛事的赛例下,赛车统一使用V10自然吸气发动机。凭借在升功率、升扭矩、极限转速、爆发力、功率重量比、燃烧效率、可靠性、平顺性等多个方面无与伦比的优势,V10发动机至今仍被F1技师奉为最完美的发动机解决方案。因此,作为F1赛车基因的延续,为了使LFA拥有究极超级跑车的性能,开发团队借鉴丰田F1赛车发动机的开发经验和相关技术,为这辆超级跑车定制设计了一台4.8升V10自然吸气发动机。
这台代号为1LR-GUE的发动机最终由雷克萨斯与雅马哈强强联手开发制造。具体的开发工作由曾在高性能车、赛车发动机方面有长期经验的发动机主管冈本高光和于上世纪90年代初主导雅马哈F1发动机开发的丸山平二领导。其他开发团队成员,则是曾经参与过丰田F1发动机或者雅马哈F1发动机研发的工程师们。相较在更早上市的IS F上仅参与2UR-GSE发动机气缸盖部分的开发工作,雅马哈此次全程参与了LFA这台赛车动力的研发工作,并将高转速、轻量化以及长时间稳定输出大马力作为最终目标。
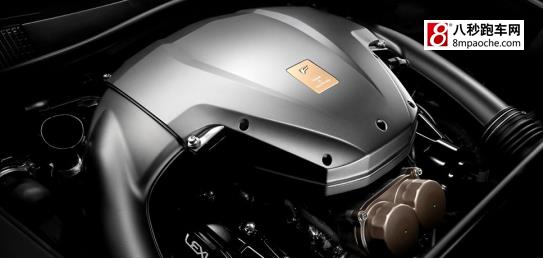
1LR-GUE发动机的缸径冲程分别为88.0毫米×79.0毫米,压缩比高达12:1。考虑到V10发动机本身的结构特性以及对发动机的体积的要求,开发团队选用了72度的气缸夹角,采用独立节气门设计,目的是减少气缸进气间的窜流,对各气缸的进气量进行精确控制,提高各气缸工作时的独立性,以此达到线性及可供预测的输出。这台全铝发动机在关键部位上使用高强度、轻量化的材料:钛合金气门、类金刚石碳化硅涂层(DLCS)超轻量化的气门摇臂、锻造铝活塞、钛合金活塞连杆等,极大地减少了发动机内部零件的运转惯性,双连通曲轴箱构造则有效降低泵气损失,为如同闪电般的动力响应提供重要的支持。它的点火顺序采用较为罕见的偶数点火,因而可以不使用常见的拼合轴颈曲轴,改用一体化曲轴,提高发动机运作效率并减轻发动机总重量。润滑系统方面,1LR-GUE使用了干式油底壳设计,使LFA在高速转弯承受高G值下,仍能保证对发动机零部件进行有效的润滑,并大幅降低发动机的重心,几近苛刻的紧凑化和轻量化设计为1LR-GUE带来了极佳的表现-V10结构的发动机竟与V8体积相当,而重量不超过一台V6发动机!
经过TMG、雷克萨斯以及雅马哈设计团队精心的设计,这台发动机具备非同凡响的性能,红线转速高达9000转/分,而电脑断油的转速更高达9500转/分,距离10000转/分仅一步之遥。在8700转/分下输出功率超过560马力,在6800转/分下能提供480牛•米的最大扭矩,并且从3700转/分开始就能提供超过90%的扭矩。将这样的输出功率与整备质量结合会发现,1480公斤的LFA比同一时代的法拉利599 GTB拥有更出色的功率重量比。更让人感到不可思议的是,发动机从怠速飙升至9000转/分的时间仅需要0.6秒,这迫使开发团队在设计仪表盘转速表时不得不放弃传统的指针式模拟表盘而改用TFT液晶表盘显示,而当发动机在红线转速运转时,铝制活塞上下运转的速度高达35.1公里/小时。LFA在这台赛车化动力的推动下,0至100公里/小时加速仅需3.7秒,极速高达325公里/小时。
200毫秒极速升挡
极快的换挡反应,并可根据驾驶模式选择的不同,将换挡速度放慢以提高日常驾驶时动力传输的柔和感、长时间连续激烈驾驶时的可靠性及尽量小的体积和重量。基于这三点开发目标,LFA最终在传动系统的匹配上选用了一台常见于赛车的序列式变速箱。
这台由爱信提供的6速ASG(Automated Sequential Gearbox,自动序列式变速箱)变速箱除了拥有相较同等性能的双离合器变速箱更小的体积和重量之外,通过安装在方向盘上的换挡拨片操控,可以顺畅紧密地配合发动机工作,其升挡时间不过200毫秒,而在降挡时能实现自动补油,使整个换挡操作如行云流水、一气呵成。
LFA的换挡拨片体现了以驾驶为中心的思路。操作右手边升挡拨片与左手边降挡拨片的力度完全不同。完成升挡操作只需要手指毫不费力地按,而要完成降挡操作则需要更用力,才能实现驾驶者与变速箱之间的互动。
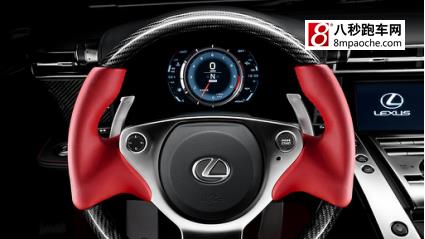
6速ASG变速箱通过扭矩传感限滑差速器驱动后轮,它是驱动桥结构的一部分并被安装在后桥上方,其作用是帮助达成理想的前48、后52的重量分配。配备微抛光变速齿轮的智能化变速箱,能实现精确换挡同时减少齿轮噪声,变速箱设有7种升挡速度,完成升挡操作的时间只需200毫秒,而降挡操作则须伴以与车速相配的降挡补油动作以获得最大限度的可控性。此外,6速ASG变速箱还提供四种驾驶模式:自动、运动、标准以及湿滑。每个模式都有其独特的换挡操作设计以及不同的发动机与制动逻辑系统,从而让驾驶着能够根据路况对系统实时加以调整。
48:52的黄金重量分配比
很多人认为50:50是高性能超跑的最佳重量分配比,但实际上能让车辆的动态潜能得到充分挖掘与发挥的重量比才算是最理想的比例。举一个简单的例子,车辆在高速行驶进行大力刹车时,会出现重心转移的现象,前轮受惯性影响将受到较大的压力,而后轮则因为车尾重量减少而出现抓地力变小,稍靠后的重心能在此时弥补车辆重心前移的现象,平衡前后轮的负荷状态。有鉴于此,LFA的研发团队在一开始便以48:52这一前后轴最理想的重量分配比例作为开发目标。
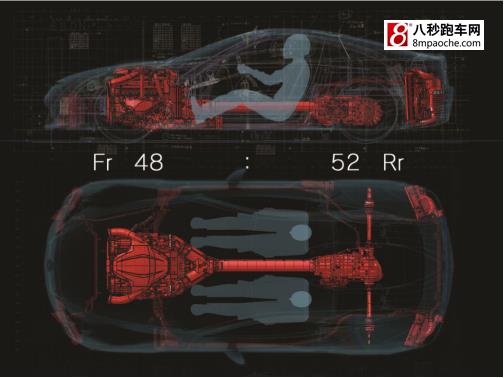
为了达成这一理想的前后重量分配比,同时保证车辆结构较为坚固,研发团队在LFA采用了前中置发动机、后轮驱动的布局方案。整台V10发动机处于前轴之后,与6速ASG变速箱借由一根刚性扭矩管相连。这根由JTEKT为雷克萨斯制造的扭矩管,以整根实心圆柱钢材,采用一般只用于飞机起落架等极端要求轻量化和强度的内径切削工法加工而来,相比一般的电阻焊接管直接制造的方式,这可以说是前所未有不计成本的做法。如此牢固的连接方式大大增加了整个动力传动系统的刚性系数。
在车身布局上,为了让驾驶者能够最良好的感知到车辆的状态,也为了在车内有乘客时,对重心的改变更小,LFA的座舱内的左右两个座位的距离仅仅720毫米,让驾驶者和一名乘客坐进车内后,也不会对重心位置相对空车时有多少改变。换而言之,LFA的驾驶员座位是基本类似赛车的位置。
另外,为了获得最佳的车身平衡,车身的主要部件都被安装在轴距范围内并降到最低距地高度。同时,铝制制动卡钳安装在尽量靠近车辆重心的位置;制动盘采用重量更轻的碳陶复合材料,较LFA赛车参加纽博格林北环24小时耐力赛(VLN)时所采用的铸铁制动盘减少了整整二十公斤的重量。
结合了前置后驱方案在可控性和直线行驶稳定性上的优势与中置后驱在操控性和灵活转向上的优势,按总工程师棚桥晴彦的话来说,就是驾驶技术还不够精炼的驾驶者也能充分享受LFA所带来的驾驶乐趣以及宽阔的安全阈度,完全符合雷克萨斯一贯的品牌追求。
基于纽北赛道开发的赛车级悬架
LFA使用了前双叉臂、后多连杆的悬架布局形式。双叉臂悬架在理论上能为轮胎带来最精确的贴地性能,而复杂的多连杆布局形式有着更深层面的考虑。这就是LFA,极端的专注造就了它。在纽博格林北环赛道上,LFA的测试团队做了大量的测试工作,使车辆在转向和底盘反应这两项对驾驶员至关重要的特性方面都有可靠的保障,同时也能平衡与协调极限速度性能、优异的抓地性和安全无忧的高速稳定性。
专为LFA研发的专属减震器,是由全球最大液压减震器制造商KYB特别为其设计和制造的型号。确保车辆在任何速度状态下直线和弯道中的减震阻尼力都不会出现丝毫的减弱。这套减震器采用带类金刚石碳化硅涂层的气缸壁,其摩擦力几乎为零,因而具备出色的响应能力。
LFA悬架系统的设计出发点就在于尽可能减轻重量,因此它采用了铝合金转向节、悬架臂以及中空防侧倾稳定杆,以此降低车辆的簧下质量。LFA可以说是诞生于纽博格林24小时耐力赛,正是通过比赛的历练,LFA 开发团队才得以总结经验,沿着车辆底盘结构的底部安装了十字防倾杆,从而打造出一个能够承受极端重力加速度的刚性平台。前后的十字防倾杆由一个格子状的中央支撑架连为一体。此外,安装于底盘前端的一根碳纤维增强复合材料制成的高效支撑杆和铝合金三角支撑架则对这些支撑系统构成了有效的补充。
超越LFA赛车的碳陶制动系统
LFA采用意大利Brembo为其特制的与赛车如出一辙的碳陶制动系统。前轴采用对向异径六活塞制动卡钳,后轴采用对向异径四活塞制动卡钳。轻量化程度极高的碳陶复合材料制动盘较LFA赛车参加纽博格林北环24小时耐力赛(VLN)时所采用的铸铁制动盘减少了整整二十公斤的重量。同时,与赛车类似,LFA为这套制动系统设计了专用的空气动力学设定,利用高速流通的空气为制动系统时刻降温,保证赛道行驶的制动力。
世界顶级热管理方案
要让一辆超级跑车真正能上赛道,其必须具备控制全车各部分所积累巨大热量的能力。机械和空气摩擦所产生的热量非常之高,如果没有有效抑制,有可能严重降低发动机输出功率,甚至还可能同时导致制动系统完全失效。在高性能跑车工程技术领域,人们往往对常见的“热源点”,如发动机和制动系统予以较多关注。但实际上,排气系统和车载电子系统也必须得到同样的隔热保护,以确保其具有较高的耐久性和可靠性。
LFA研发团队想出了一套全面性解决方案用于应对这一挑战。其中一个关键机制便是采用一个大型的散热通道,该通道以底盘前部为起点,贯穿车身中央通道,然后再通过尾灯下方的双散热孔一直延伸出车辆尾端。该散热通道结构可以有效清除源于多种机件摩擦而久留不散的热量,并将这些热量从车尾排放出去,从而防止碳纤维增强复合材料车身、动力传动系统和电子元器件遭到毁坏。
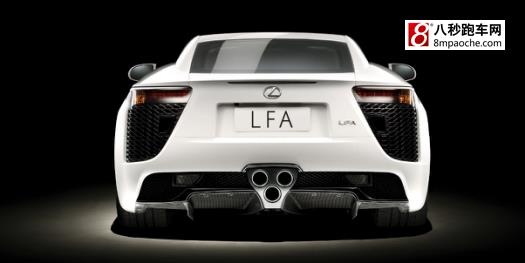
位于车尾的双散热器通过安装在后轮上的大型进气口直接抽取空气,这样不仅可以对发动机起到最大限度的冷却效果,同时也有助于实现最佳动态平衡。此外,一个大容量离心式水泵被安装在发动机中的较低位置,它可以通过大型的轻量化铝合金管道将热量输送到散热器中。作为一种补充手段,一个大型水冷式油冷器被安装在V形斜角水箱内部,水箱则通体包裹着导热薄板,以便提供高效和持续的润滑冷却。
当车辆在赛道上高速行驶时,制动系统能否有效冷却至关重要。位于前保险杠内和发动机舱盖下方的导气管将新鲜冷空气输送给前制动系统,从而起到冷却效果。抑制制动系统温度过高可以有效防止制动系统热衰减,这样即使在严酷的路况条件下仍能保证驾驶者有连贯一致和安心轻松的制动感受。
乘用车中最接近于F1的声浪
这是汽车厂家首次将V10自然吸气发动机调成一具不停演奏的乐器,使驾驶者与LFA之间产生强烈的共鸣以及交流。雅马哈根据多年的乐器生产演奏经验,认为音量、音色乃至轻微的变化和即时变化都能更好地协助演奏者演奏出动听悦耳的音乐。在LFA上,如果把驾驶者比作乐器的表演者,LFA就化身成了传播悦耳声浪的介质,而驾驶者的乐器自然就是隐藏在发动机舱盖下的那颗4.8升V10发动机。
稳压箱是制造发动机声浪的一个必要组件,因此雅马哈要对其做认真的调音,以获得最佳的声浪效果。借鉴自现实乐器的设计,稳压箱的侧面都做得非常坚固,同时还在前半部加装了横肋,以便能产生更具力度的吸气声浪。
燃烧后的废气自发动机左右两组气缸中排出,各自经过单独的等长大口径排气歧管,在这过程中不仅可以提升扭矩水平,还会制造出音质清脆的声浪。在通过催化转化器后,两股废气流将经过一对副消声器,然后在车辆后部与安装在后置变速箱背面的一个多级钛合金消声器中汇成一股。
钛合金后置消音器包含有一个由阀门驱动的构造,它可根据发动机转速对废气流进行引导。发动机转速在3000转/分及以下时,阀门保持关闭以便引导尾气通过多个排气管谐振腔管,从而声浪较为平和优雅。发动机转速 3000转/分及以上时,阀门开启以便让尾气通过单个排气管谐振腔管,从而声浪类似女高音般的高八度。V10发动机在9000转/分以上的声浪彻底征服了棚桥晴彦,这种极其接近F1赛车高亢嗓音的美妙音色被他形容为“天使的咆哮”,并成为了LFA最为著名的标志之一。
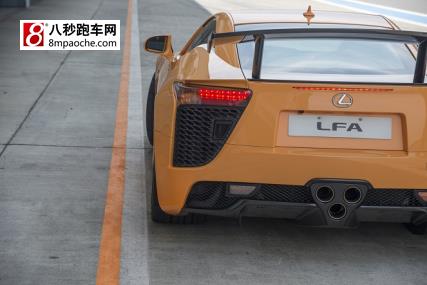
发动机进气和排气系统的声浪都要通过一条条精心设计的声道进入 LFA 的驾驶舱。主声道始于稳压箱并从主仪表板下方接入驾驶舱。另外两个声道则对其构成补充,其中一个在前罩板开口处,另一个位于下方的反光镜处。这些声道可确保驾驶者坐在欣赏由发动机演绎的一场立体环绕式声响音乐会的中央位置。
极近完美的空气动力学外观设计
LFA线条简洁干练、富有肌肉和运动感,它集超级跑车的外观造型与雷克萨斯的“L-finesse”设计理念于一身,从而构成一个各部分顺畅衔接、紧密结合的有机整体。
流线形外观的LFA兼具低车身和充满力量与运动感的设计,它的每一条曲线和每一个角度都透出超级跑车的风范。尽管在外观设计上突破了既有的模式,但人们依据对雷克萨斯“L-finesse”设计理念的秉持,还是一眼就能认出LFA身上的雷克萨斯基因。“L-finesse”设计理念深深根植于传统和当代日本文化中,它包含了三个核心元素:纯-“敏锐的极简”;妙-“令人着迷的优雅”;预-“完美预知所有需求”,它代表了日本招待的体验与关怀。LFA从头到脚的线条都十分连贯、流畅且凹凸有致。
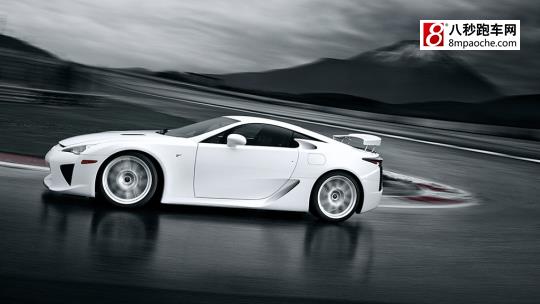
碳纤维增强复合材料具有重量轻、强度高的特点,正是这一特点赋予了LFA设计师更高的设计自由度,使他们能够打造出利用金属材料根本无法制成的各种造型、曲线和边缘。举例来说,倘若用传统的金属材料制造车身,那么就不可能打造出LFA车尾突出的尾缘。
LFA的流线形造型是数百小时风洞试验和不间断的计算机建模的结果,其中后者利用了功能强大的计算流体动力学程序设计。最终定型的超级跑车不仅在外观上有较高的回头率,而且空气动力学性能也相当出众,从而使得车辆在拥有极佳高速稳定性的同时亦具备良好的抗风阻性能。尾翼收回时,LFA的风阻系数仅为Cd 0.31。
LFA底部和车身周围的空气动力学组件都经过造型优化,在设计上实现了对气流的精准控制,并且它们的安装位置也都达到了预期效果。比如,车头中央的进气口旁边安装了橡胶密封垫,防止过多气流进入发动机舱。又如,A柱与挡风玻璃交汇处配备小型扰流鳍片,其功能在于提高车辆直线行驶和遭遇侧风时的稳定性。带扩散板扰流作用的自动扬升尾翼根据车速调整状态。低速时它会处于收起状态,但当车速提高到80公里/小时,它将自动调整到位并产生下压力,以保证车辆的稳定性。
此外,LFA车身底部经过专门设计,完全平坦,因而可以产生强大的下压力。车底气流速度相对车辆上方的气流速度要快一些,两者之间形成的较强压力差可以使车辆牢牢地“扣”在路面上。
史无前例的高科技驾驶舱
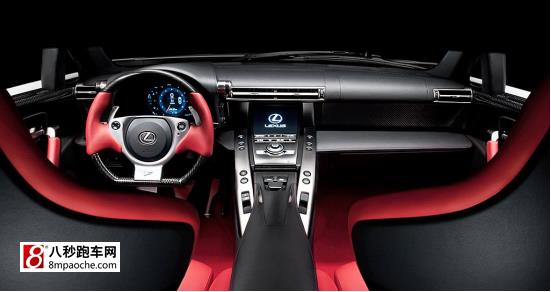
打开LFA的车门,一个轮廓低矮却不失吸引力的驾驶舱展现眼前,它经过巧妙精心的设计并且采用最好的材料以手工方式组装而成。富有人情味的统一,是LFA最让人感动的地方。它注重的不仅仅是机械性能,更是那种亲密无间的人车交流。先进而人性化的仪表界面消除了驾驶者与机器之间的沟通障碍,清晰明确、逻辑性极强的行驶数据时刻为驾驶者提供准确而实用的辅助信息。电光火石间,让人尽享超级跑车的极致乐趣。特别值得一提的是,由TFT液晶显示屏和电机驱动移动表环组成的中央转速表即使今天看来也极具科技感,尤其是金属环中的多层树脂镜片能够表现出层叠的效果,在切换驾驶模式时,仪表盘的显示效果也随之转换。
将驾驶舱一分为二的可升降式中控台容纳了 7 英寸的一体化显示屏以及采用智能化区域性控制的空调系统与信息娱乐系统。中控台采用缎纹金属件与真皮做饰面,同时两侧还有十颗哑光黑色的按钮作为搭配。LFA还采用了创新型Remote Touch多媒体信息操作系统,它位于驾驶员的落手处,能提供最佳的控制、操作便利性。
LFA真皮包裹的座椅采用了契合人体骨骼构造的设计,拥有上下分开式的座椅靠背、突出的侧支撑和8向电动调整装置。座椅被安放在轴距中心的位置,并且其横向轴线也尽量贴近车辆重心。这种布局方式让驾驶者能够对车辆运动状态的变化产生较为直观的感受和反应。
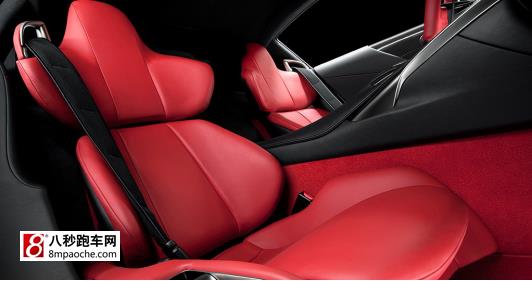
驾驶舱内饰采用质地柔软的手工缝制真皮或明暗线缝纫的Alcantara 材料,同时搭配丝光及哑光碳纤维增强复合材料和缎纹金属件。挡风玻璃下方的哑光涂层采用宽大的网眼形碳纤维材料,其用途是减少反射的日光,而中控台两侧、方向盘以及车门板则覆以碳纤维丝光涂层。当然,可供LFA车主选择的内饰材料与色调十分广泛,足以帮助他们打造真正个性化的驾驶舱。虽然执着于赛道,但LFA在豪华性上却并未有丝毫让步,双区域车内空调控制系统、基于硬盘驱动器的卫星导航系统、专为用户定制设计的带有12个扬声器的Hi-End级Mark Levinson音响系统等豪华配置,让LFA不仅是雷克萨斯运动精神的图腾,更同样是展示雷克萨斯一贯豪华舒适的杰作。
LFA纽博格林版
LFA正式立项后不久,LEXUS雷克萨斯就把LFA重要的试验场定为位于德国境内的纽博格林北环。身为LFA试车负责人的成濑弘,早在LFA项目立项之时就已经极力推崇被称为“绿色地狱”的纽博格林北环赛道,认为它是开发、测试和检验LFA最佳的场所之一。围绕纽博格林赛道研发制造的LFA,在2010年3月15日也终于推出了专属于赛道调校的版本-纽博格林版。这一特殊版本是在标准型LFA的基础上做了数项改进,通过全面优化提升赛道性能,限量50台,并属于500台生产计划之内。
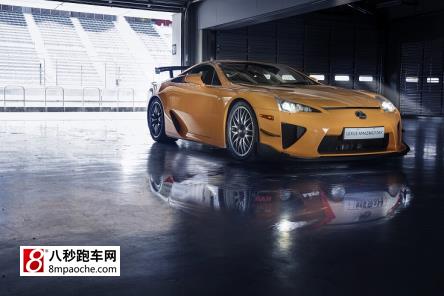
LFA纽博格林版的4.8升V10发动机经过重新调校,输出功率达571马力,比标准版增加了11马力。额外的功率使得车辆需要更大的下压力。为了让车子紧贴赛道,碳纤维增强材料的固定式尾翼被安装在了车上,而位于前保险杠两侧的碳纤维增强材料扰流鳍板也能提供更强的下压力。同时,6速ASG变速箱的换挡速度也被进一步缩短,从标准版的0.2秒精进至0.15秒。再加上换装了针对赛道驾驶而强化调校的悬架系统和定制轮胎,LFA纽博格林版的操控性和稳定性得以再次强化。
2011年纽北圈速最快的日本跑车
在为LFA进行过大量研发测试的纽博格林北环赛道上,职业赛车手和LFA测试驾驶员饭田章驾驶LFA纽博格林版于2011年创造了7分14秒64的圈速记录,这使LFA在当年成为纽博格林北环圈速最快的日本跑车。更重要的一点是,在刷新圈速时,LFA仅使用了复合标准路面法定规格的普利司通RE070轮胎,并没有为圈速成绩而更换抓地性能更好的半热熔轮胎。
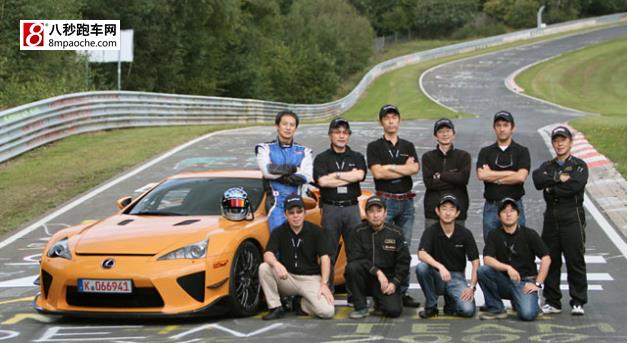
“F”永远的标志
在汽车发展史中,高性能车一直代表着梦想和信仰。这些最好的汽车始终拥有同时代车型中最出类拔萃的、令人动情的力量。虽然LFA已经不再生产,但这并不代表它已经走进了历史的滚滚车轮。世界上没有几个汽车厂家能够从无到有制造出一辆旷世超跑,它证明了雷克萨斯和丰田集团有能力问鼎巅峰的强大技术实力。更重要的是,LFA扮演了催化剂的角色,促进了工程和产品开发流程的优化,丰田生产体系由此经历了一场变革,工程师、设计师和生产线上的同事开始紧密合作,这是一个最终让全车系都受益的过程。
雷克萨斯在研发和生产LFA超级跑车过程中,积累了大量的技术经验,尤其是碳纤维增强复合材料的生产工艺,以及打造充满驾驭激情的设计理念。当然,LFA也为雷克萨斯运动品牌“F”的创立树起了先行者的印象,将带领“F”品牌为消费者带来别具风格、充满激情的驾驭体验。
(转载请注明来源:八秒跑车网/www.8mpaoche.com 责任编辑:milk,Jack)
“八秒跑车网”微信公众号,扫一扫,最新资讯随手掌握。